A Closer Look at Blasting Equipment Installation
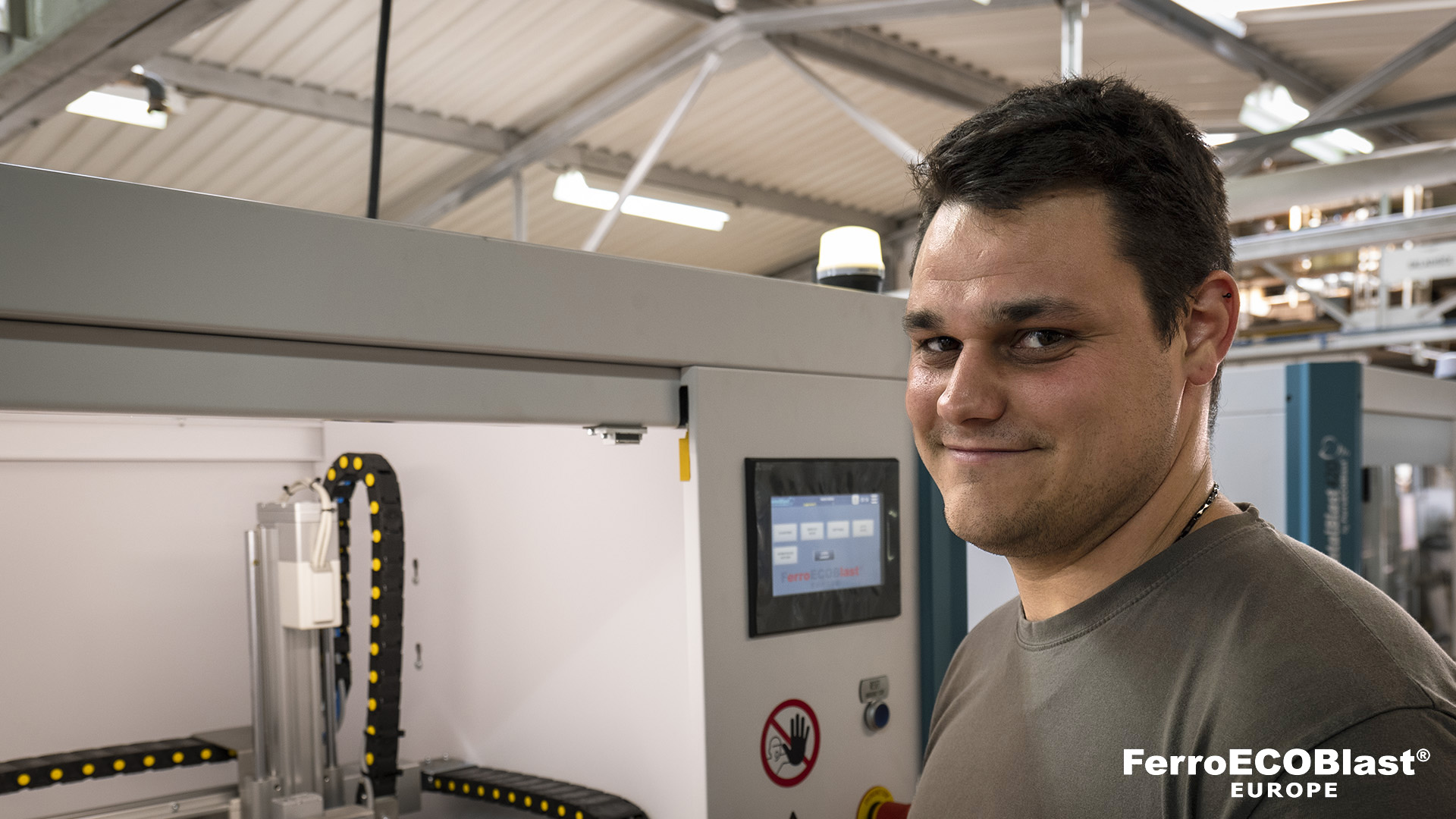
Greetings to all from an installation technician. Who am I? Matic Kuhelj, Head of Installations at FerroČrtalič. Some of my friends think I have a dream job, travelling a lot and working out in the field all around the world as I am. At the same time, I have an interesting job, one that makes me happy. All this is in fact true – but at the end of the day, one still needs to deliver results, which in my case is installed and operational equipment designed for technological surface treatment processes. Our installations, both at home and abroad, are carried out to high professional standards, drawing from our previous experience and technical know-how. Through our ongoing operations we have gained invaluable experience and satisfied customers.
When it comes to assembly and installation, we face a variety of challenges. Our mechanical design engineers work on planning and designing the machine, where appearance is very important. Assembly and installation, however, come at the end of the product development process, so any defects occurring during the manufacturing processes often go undetected until the product has been assembled.
I recently completed the installation of state-of-the-art automated equipment for the surface treatment of dental implants. It was a DentalBlast 900, with an hourly throughput of 240 implants and measuring 3000x1800x2400mm in size. Currently available in the global market are mostly manual or semi-automatic implant treatment machines. Our development team has therefore focused in particular on the quality and control of the treatment process, and for this purpose they have developed a fully automated blasting system specifically for dental implants. The equipment consists of two parts. The first part is the blasting booth, where the implant handling and blasting process is performed, and the second part is the abrasive medium recycling system. In the first stage, the assembly and installation team put up the frame and construction, then continued with the assembly of the interior, which includes components such as a table, rotating unit and manipulator device. The installation of the electrical cabinet was followed by the installation of compressed air and electrical components and electrical wiring. All manipulation processes in the DentalBlast 900 dental implant roughening machine are fully automated and controlled. Finally, the final inspection and testing of the equipment takes place. The equipment testing took several days to complete because it is an automatic solution where the coordinates for the picking and placing of implants need to be set up at the very beginning. For the machine to operate flawlessly, the position of the nozzles and other minor details were then fine tuned as well.
The machine is fed by an operator who places the implants tray in the dedicated space on the left side of the machine. When the machine runs in automatic mode, the manipulator carefully picks each implant and places it in the blasting position. After the blasting and cleaning is completed, a final inspection is performed using a color camera, which records whether the implant is properly treated or not before being returned to the tray by the manipulator. In this way, all the previously prepared implants are roughened,cleaned and controlled. This process can run continuously for several hours without the presence of an operator.
During the installation, technical challenges may also arise for us, installation and assembly engineers. It was on this machine that during installation we identified the need for service and maintenance access openings. When setting the position of the table, which is a very demanding task, we found that it would make our work easier if there were a service access opening in the lower section of the booth. Working with our development and technology department, we have developed a solution that is user-friendly, functional and, of course, safe to use.
Installations in our home country are much easier and faster. But what is it like to install or put into commission our blasting equipment abroad? Apart from making many new friends and meeting beautiful girls, it can also be quite challenging. It requires the ability to adapt to the environment and people, knowledge of foreign languages, competence, technical know-how and, of course, great resourcefulness and ingenuity in all areas.
If we happen to meet somewhere around the world, make sure to say hi! Regards, Matic